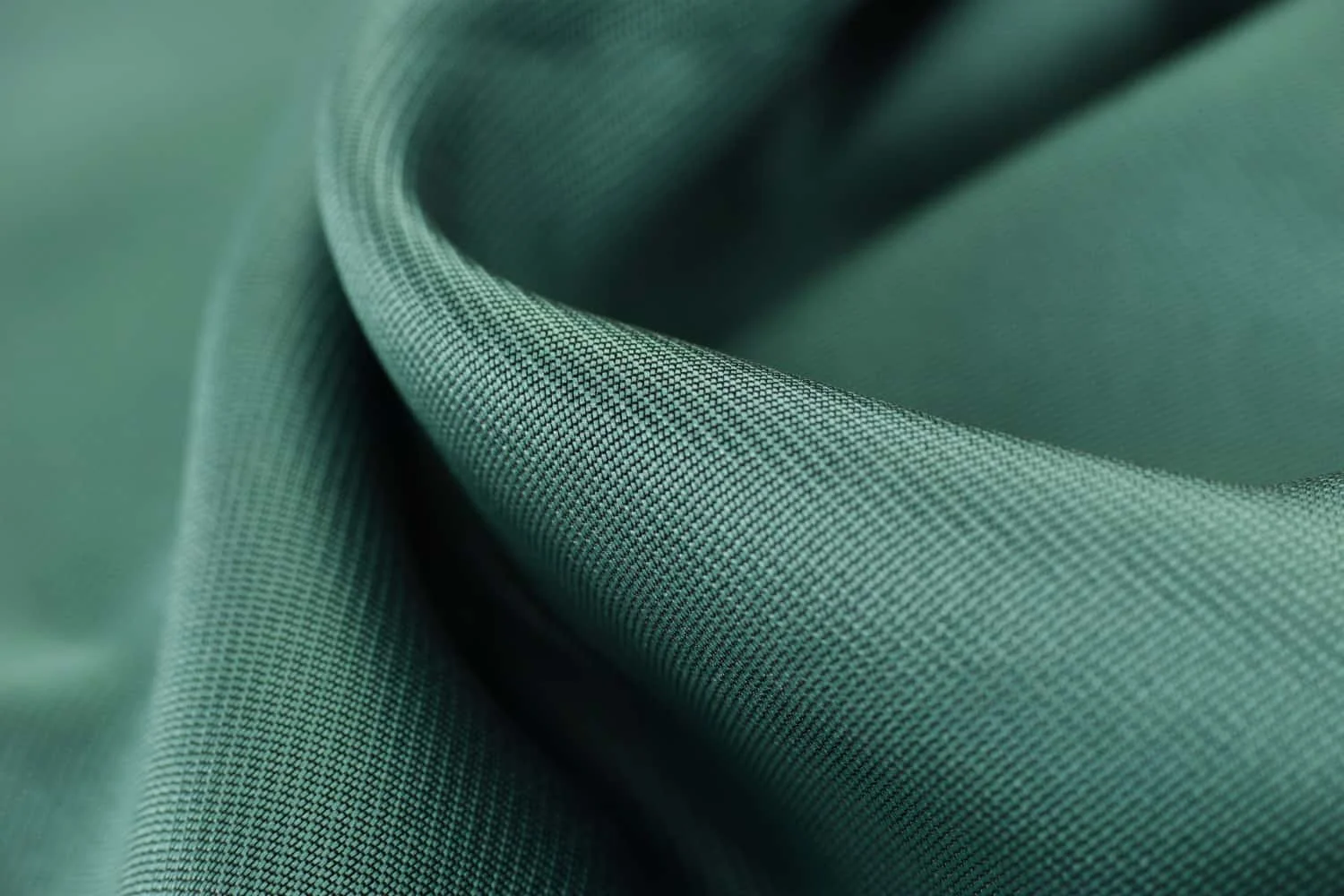
Shrinkage of Knitted Fabric: Causes, Effects, and Management
Introduction to Shrinkage in Knitted Fabric
Losing or shrinkage is very rampant in textlies and more so when it comes to fabrics made of knitting. It is a well understood and established fact that knitted fabrics offer stretchability as well as flexibility of the fabrics and thus are used widely for manufacturing different types of garments and products. But, it is a fact that knitted fabrics cause shrinkage after washing it or coming in contact with heat. It is Therefore, very crucial to understand what causes shrinkage in knitted fabrics, and the consequences that are likely to arise due to shrinkage. The focus of this article is giving details on shrinkage; its influence on fabric performance and ways of mitigating / preventing shrinkage.
A General Interpretation of the Retirement of Knitted Materials
The main source of shrinking in knitted fabrics can be broadly explained by the type of fibers used and the way the fabric is knitted. Because they are organic, fabrics like cotton and wool are especially vulnerable to shrinkage owing to their capacity to absorb water and the kind of fibers used in their manufacture. When these fibers are exposed to water, especially at high temperatures, they expand and shrink causing the size of the fabric to decrease. Furthermore, exposure to heat such as that given out by dryers or through ironing increases shrinkage as it alters the look of the fiber.
Non- woven fabrics can be defined as having a woven structure while knitted fabrics are characterized by a more malleable look because of their looped look. They also make knitted fabrics more sensitive to heat or moisture that leads to shrinkage of fabric structure. Loops in knitted textiles have been found to contract when the fabrics are submerged with water and/or exposed to heat which would consequently result in shrinkage of fabric dimensions. Knitting process also impacts shrinkage and yarn tension is one of the factors that can be influenced. The fabrics that are knitted with tension possess low shrinkability because the fiber is fully extended than fabrics that are knitted with low tension hence have high shrinkability.
Types of Shrinkage in Knitted Fabrics
Shrinkage in knitted fabrics can be categorized into two types: fibrillar contraction and relaxation shrinkage. Dimensional change is defined as the magnitude of alteration in the size of the fabric, normally both width and length, after washing the fabric. Such shrinkage is typical of cotton-based fabrics, though can also appear in blended fabrics containing synthetic materials, if treated inadequately. In contrast, developmental shrinkage is when the microfiber material relaxes some of the tension that characterizes fabrics that undergo this process during their production phase. This kind of shrinkage is mostly in the width direction and most obvious in fabrics made from yarn knitted under tension.
Influence of Shrinkage on Knitted fabric
Shrinkage will always affect the appearance and usefulness of knitted fabrics as much as it will have an effect on their physical appearance. For garments in particular, shrinkage results in distortion of the shape of the final product and size differ from MOST customers’ expectations. This is particularly so given the fact that sizing is critical in the fashion industry where insignificances may cause significant problems. At times the shrinkage process leads to garments that cannot fit the body any longer thus cannot be worn.
From a manufacturing perspective shrinkage results in inefficiencies within the manufacturing process. For example if the fabric shrinks during the finishing process and to a very high extent then extra time and money may be needed to correct the position of the pattern or the final size of the garments. This can cause some productive delays and consequently raise the amount of production expenses. However, shrinkage is not good for the knitted fabrics because they may reduce the durability of the fabric. When the fibers contract the fabric loses its elastic properties and becomes less strong and could easily wear out.
Managing Shrinkage in Knitted Fabrics
Here are some measures that the manufacturers can adopt in order to minimize or manage shrinkage in knitted fabrics. The most frequently used practice is pre-shrinking, also called sanforization. Pre-shrinking may be done by various methods including dry heat treatment. This process includes washing and drying the fabric, in a more controlled environment before the material forms a garment. Thus, the shrinking process has to be made prior to sewing to achieve the results when all residual shrinking of the fabric is already produced during washing or drying of clothes and not afterwards as part of the final product.
One of the common strategies of handling shrinkage loss is the application of fiber blends. Cotton and polyester blended fabrics will shrink to a lesser degree than fabrics just from cotton or just from polyester. The synthetic fibers remain resistant to shrinking more than natural fibers therefore using them has a balancing effect on the fabric and its dimensions. Furthermore, there are some heat-setting treatments which can be applied to some types of fibers, for example, polyester or nylon, the fibers are locked in place, and therefore shrinkage drawback when contacting with water or heat is minimized.
Another important determinant of finish treatment shrinkage is the choice of the right finish. Various treatments such as chemical softening, heat setting and steaming relaxation or finish can minimize the tension in the fabric and thereby retard any subsequent shrinkage. Some manufacturers also use surface treatments of knitted fabrics to make them less shrinkage or other kinds of wear. These treatments also contribute an extra barrier of protection and enable the material to retain the shape on intended dimensions.
Awareness to Whom and Care Information
For consumers, there is the appreciable aspect of how they can avoid too much shrinkage of their knitted fabrics. To avoid shrinkage one should wear knit garments in cold water, wash in a gentle cycle, and do not use high heat to dry them. It is also preferred not to use a tumble dryer to dry the knitted fabrics’ products because the hot air shrinks the fibers.
Care labels attached to garments serve as an important reminder to consumers of the right way in which they should handle the garments,especially as regards washing,so that the material and color does not fade off or shrink. With these care instructions in mind consumers can ensure that they do not shrink their knitted textiles as well as take care of their garments in order to make them last longer.
Conclusion
El- sized fabrics are one of the common problems that affect fabrics’ performance, garment dimension and productive efficiency in the production process of knitted fabrics. It is therefore important for both the manufacturers and the consumers to understand the causes and forms of shrinkage as well as the corrective measures of the contracts. However, through pre-shrinking methods, use of fiber blends, and proper finishing treatments the effect of shrinkage could be minimized in such products to help manufacturers come up with the right quality products. For consumers, it is useful for them to adhere to the correct wash and care instructions to ensure the fabric’s size and shape is retained alike. Still, if the right strategies are put in place, the shrinkage matter can be well dealt with so that knitted fabrics can be responded as found best suited for different uses.
Keep an eye for more news & updates on The Fashion Star!